Reynders chooses Vetaphone for surface treatment
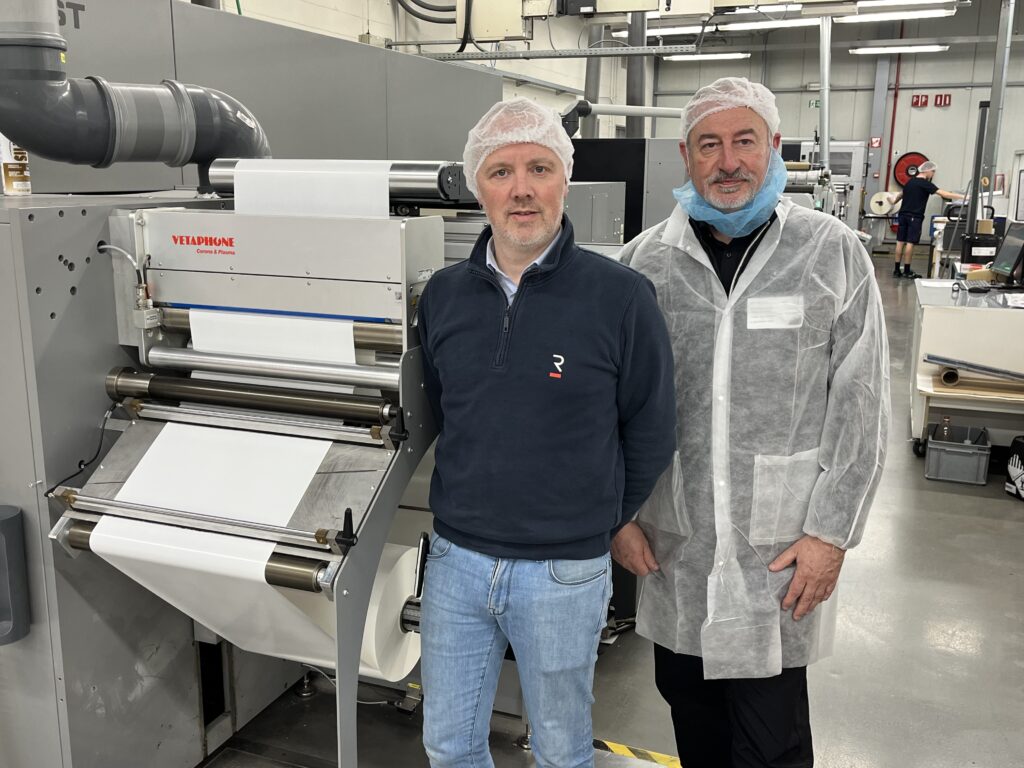
With eight production sites in six countries, the family-owned Reynders business has been supplying the label industry for more than 50 years and is now under third generation management. Established in 1956, and headquartered in Boechout, Belgium with plants in France, Poland, Spain, Germany and India, the company now employs more than 700 people of which approximately half that number work in Belgium.
The company, which is managed by a team of five people representing Sales, Finance, Production and two additional family members, Sébastiaan Reynders (Buying, Planning & Logistics) and Bart Reynders (Sales Manager Pharmaceutical Labels), has been renowned for the variety and quality of its printed output and innovative techniques since it began to specialise in labels in the 1980s. The first contact with Vetaphone came more than 30 years ago when Marc Reynders and Dirk Den Haese of Vetaphone Benelux began discussing how best to equip the company’s converting lines, mostly ABG and GM machines and in the early days Nilpeter printing presses, with reliable and efficient corona technology.
Since then, Vetaphone has installed more than 50 of its corona units at Reynders’ plants with more due for installation. Speaking for Reynders, Operations Manager Joris Mermans said: “What we particularly appreciate with Vetaphone corona is its low maintenance requirements. We very rarely have any issues with the easy access cartridge system and if we do, then spare parts are readily available and delivered quickly.”
Responding for Vetaphone, Dirk Den Haese commented: “Surface treatment might be only an ancillary part of the overall production process, but it’s one of the most vital links in the chain if you are dealing with film or foil materials. Poor quality corona coverage will pose quality issues downstream and can involve costly reprints which neither converters nor customers can afford.”
Most of the label capability at Reynders is 330mm and 550mm web width, with 2kW corona power for the oldest machines and 4kW for the most resent printing presses with higher speeds and more demanding substrates. Reynders is using a mix of machine manufacturers’ technology including Gallus and Mark Andy presses that produce self-adhesive labels, sleeves, flexible packaging and IML for markets that include pharmaceutical, cosmetics, food & beverage, industrial, automotive, chemical and household & garden.
The company prides itself on its sustainability record, and operates under the mantra of: ‘Smart, Safe & Sustainable’ stating that a green future begins with the choices we make today. As Joris Mermans explained: “Sustainability is in the process, not just in the materials. Producing labels as efficiently as possible combined with care for the environment and its employees is what sustainability means to Reynders.”
Making the right choice is a key part of ‘being green’. For instance, a paper label is not always the most environmentally friendly if, when applied to a PET bottle, it makes recycling more complex. Likewise, cartons can often be used only once, whereas plastic packaging can have multiple lives. Reynders label printing works by responsible sourcing, reducing, and recycling. In addition to a return on investment, the company says it strongly focusses on all possible environmental effects.
As Dirk Den Haese concluded: “Plastic packaging has an increasingly poor reputation in the eyes of the public, but this is largely undeserved because it offers significant advantages that paper-based packaging cannot. At Vetaphone, we are constantly working with new and more ecologically friendly substrates, and value the cooperation we have long held with Reynders to meet their environmental requirements.”