Tension in the Air: How Corona Treatment Enhances In-Mold Label Printing
Published By: Baldwin
The packaging print market is experiencing significant growth, driven by rising demand for flexible packaging, labels, boxes, and wrappers. This expansion has led to the emergence of various printing processes—Digital, Flexographic (Flexo), Rotary, and Offset—each with its unique applications. One commonality among these methods, especially when printing on plastic films, is the need for corona treatment. This crucial step ensures effective ink adhesion, enabling high-quality print outcomes and proving vital in supporting the growth and diversification of the print industry.
Defining and Understanding Corona Treatment
Corona treatment is a process that modifies the surface tension of plastic films, allowing inks to adhere more effectively. Without this treatment, the adhesion between ink and film is weak, leading to blurred prints and easy peeling. Corona treatment involves exposing plastic film to a high-voltage electric discharge, creating a corona of ionized air. This process increases the surface energy of the plastic, typically measured in dyne levels, allowing for a stable connection between the film and the ink.
Various factors influence the design and power of corona treaters, including machine speed, type of plastic film (such as PP, OPP, or PE), and the type of printing ink. Higher machine speeds require more power to maintain the necessary surface tension, while different plastics have varying energy requirements. Solvent-based inks typically need lower dyne levels (38-40 mN/m), whereas water-based inks require higher levels (42-44 mN/m). UV-curable inks, commonly used in In-Mold Labeling (IML), demand even higher surface tensions, often exceeding 44 mN/m for optimal results.
Corona Treatment for In-Mold Labels with Offset Printing
In-Mold Labels (IMLs) are thin labels made primarily from polypropylene (PP) plastic films, fused into containers through injection molding. IML offers several benefits, including seamless integration into the molded product, no need for additional adhesives, and easy recyclability, leading to increased demand for these types of labels. Offset printing is particularly well-suited for IML production due to its high-quality prints, exceptional detail, and color accuracy. However, a critical step in IML printing is the application of corona treatment to ensure proper ink adhesion to the plastic film.
For offset printers transitioning from commercial printing to IML production, corona treatment can be a new technology requiring adjustments to existing equipment. The most common setup involves placing a corona treater on a sheeter before the press, allowing for continuous treatment of the unwound film. Some sheeters are designed with built-in space for corona treaters, making it easier to upgrade existing lines. Even older sheeters can be modified to accommodate a corona treater, typically just after unwinding but before the film moves into the sheeter.
Companies like Baldwin Technology offer tailor-made solutions for offset printers, providing corona treaters designed for robust and simple operation. These treaters feature easy-change systems for straightforward maintenance, allowing operators to clean high-voltage electrodes on the workbench. The design and power of these treaters depend on machine speed, plastic film type, and ink type, ensuring optimal surface tension and high-quality print results.
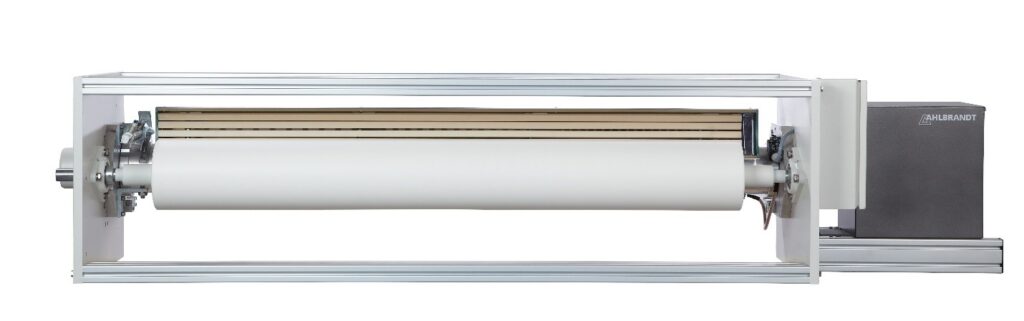
Corona Pure surface-wide treatment system.
Conclusion
Corona treatment is a critical component in the successful application of offset printing for IML production. By ensuring proper adhesion between inks and plastic films, this treatment facilitates high-quality, durable prints with exceptional detail and color vibrancy. As the demand for IML continues to grow, it is essential that offset printers integrate corona treatment to meet the evolving needs of the packaging print market.