MEGNAJET’S FLUID MANAGEMENT SYSTEMS BRING PRECISION AND CONSISTENCY TO ARROW DIGITAL’S PORTFOLIO
By: Megnajet
Kettering, 3rd December 2024: Megnajet is supporting partner Arrow Digital’s growing portfolio, with several of its fluid management systems providing the increased productivity, efficiency and control its machines demand.
With over a decade of expertise in fluid control and conditioning, Megnajet’s solutions offer the precise regulation of meniscus pressure, temperature and recirculation rate for a range of applications.
Driven by a shared vision to meet the evolving needs of the digital print industry, the collaboration between both businesses centers around efficient and consistent print quality for Arrow Digital’s fast-paced customer markets. Thanks to this partnership, downtime for both short-run jobs and large-scale operations has reduced significantly, driving improvements for Arrow Digital’s customers.
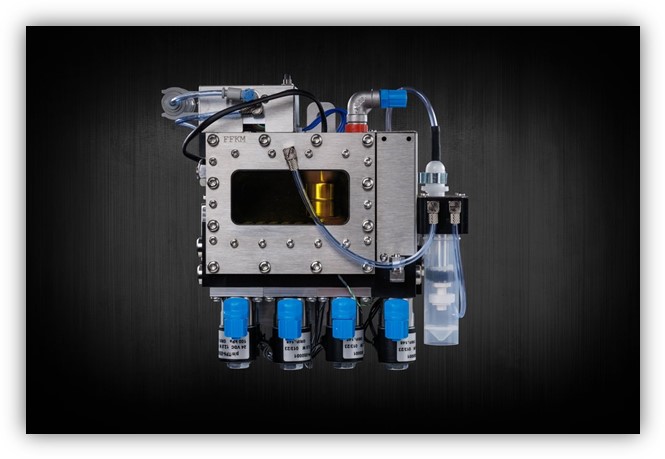
With a legacy of excellence spanning decades, Arrow Digital stands as one of India’s foremost manufacturers of digital printing and finishing machines, providing innovative solutions across diverse sectors such as labels, flexible packaging, sign and graphics, and textiles.
The digital print manufacturer utilises both Megnajet’s HiValve LFR and RackFit Gravity fluid management systems in its ArrowJet UV and ArrowJet VDP machines, which stand out among competitors for delivering high quality labelling and embellishment printing.
For the ArrowJet UV’s packaging and label printing applications, where sharp imagery and productivity are essential, Megnajet’s HiValve LFR enables the production of vibrant, high-quality prints at scale. Its innovative design supports fluid supply for up to five individual outputs and is compatible with all industrial highflow printhead types.
In addition, the HiValve can turn off individual printheads for maintenance and shut down without loss of fluid, an important selling point for the efficiency of Arrow Digital’s machines. As a result, it can meet a wide range of customer demands and continually provide clients with a reliable printing experience.
“Megnajet stood out from competitors for its reliable solutions that deliver precision and efficiency,” said Sam Patel, CEO and Managing Director of Arrow Digital. “Its fluid management systems address the challenges we previously faced of consistent fluid control and waste reduction. Megnajet didn’t just understand our goals, it aligned with them.”
In November, the ArrowJet UV, equipped with Megnajet’s HiValve, was showcased at Labelexpo India. Spanning over 18,000 square meters and with 250 exhibitors, it is the largest label and packaging industry event in South Asia. The new ArrowJet machine saw significant interest and marked a milestone in the companies’ developing partnership.
Mike Seal, General Manager at Megnajet, concluded, “Arrow Digital’s dedication to quality across its impressive portfolio along with our commitment to innovative and reliable products makes this the ideal partnership. We are delighted that they saw such success at Labelexpo India with the Arrowjet UV and its use of our HiValve LFR, and look forward to supporting their continued business growth.”
About Megnajet
Based in the UK, Megnajet is a fluid management specialist, providing unrivalled solutions for customers worldwide.
With over a decade of experience and a product range covering a wide range of industries, applications and industrial printhead types, Megnajet’s team provide solutions from application concept through to full customer commercialisation, delivering innovation in ink systems.
Megnajet systems are light and compact, easy to integrate with rapid start up and settle times and are the smallest fully integrated ink systems available. In house manufacture ensures units are customised to suit different fluid types and applications, giving OEMs and integrators the ability to add reliable and precise industrialised fluid management control into their systems.