Amherst Label, an Inovar company, adds third Domino press
Published By: Domino
Amherst Label, an Inovar company, located in Milford, New Hampshire, USA, has added their third Domino N610i digital UV inkjet, with the installation of their second MPS EF SYMJET ‘powered by Domino’ hybrid press in February 2024.
“We have 55 full-time employees and we’ve added 250 new customers in the last two years. Our key objective is to take great care of our customers, provide great opportunities for our employees, and use technology to continue to grow. Today, we have four flexo presses, one Domino N610i digital roll-to-roll, and two MPS-Domino (flexo/digital) hybrids. So, it’s really exciting to see our growth. And last year, we merged with Inovar Packaging Group, which is a great fit for us,” says Nye Hornor, president of Amherst Label. With 11 current locations, Inovar Packaging Group is creating a world-class commercial enterprise by building a platform to drive scalable and sustainable growth.”
Digital Drivers
Katie Putnam, Prepress & Digital Print Supervisor says, “Several years ago we started to see more versioning, more SKUs, more specialty labels, shorter runs. Customers were looking for higher quality. Nye adds, “The other big thing was turnaround time. And customers started asking for variable information. So, everything was really pointing us in the direction to add digital.”
Amherst Label’s first digital press was the Domino N610i digital UV inkjet label press, installed in July 2016, followed by their first MPS EF SYMJET ‘powered by Domino’ hybrid press in March 2021. A driving factor for adding the MPS-Domino hybrid was not only needing additional capacity but also the desire to print and convert in a single pass, all inline, while being able to add embellishments, varnishes, cold foil, and more. Nye says, “With being able to print and convert inline, we are saving a tremendous amount of time by doing the process in one step versus two steps. So, we have more throughput, more productivity. All these benefits are a Domino effect.”
Is there a ‘Domino Difference’?
“The Domino has been a great addition to our fleet of equipment,” says Nye. “There are several key advantages of the technology. First is the opacity of the white. Second is speed. I have talked to converters that have other digital equipment running half the speed that we are. The other day, we were running at 65 meters/minute (213 ft/minute). And it’s not just speed for printing, but speed to the customer. Third is color gamut. With our CMYKOV+W, we can hit almost any color. And fourth, and most important, is the quality. When we sent out the testing for samples to be done, the Domino samples that came back to us were the best of any digital printing provider. Domino just really stood out, and we knew we would be excited to send that quality to our customers.” Katie says, “I agree. And another one I will add is color consistency. That is a huge factor. So, whether it’s running 20,000 feet of product this month for a customer or only 5,000 of the same label next month, we know it’s going to match.”
Beyond the Press
Nye concludes, “We have been very satisfied with Domino. We trust the Domino technicians, and they trust our people, and it’s a great back and forth in understanding each other’s needs.” Inovar is clearly one to watch over the next couple of years as the company continues to acquire, invest and expand its geographic footprint, capacity, and printing capabilities.
About Inovar Packaging Group
Inovar is one of North America’s premier label printing and packaging solution companies. From its headquarters in Dallas, Texas, Inovar produces packaging products for many of the nation’s leading brands across multiple industries. Inovar invests in the most current technology to help clients meet the demands of the marketplace and demonstrates a passion for providing unsurpassed quality and service. For more information, visit www.inovarpackaging.com.
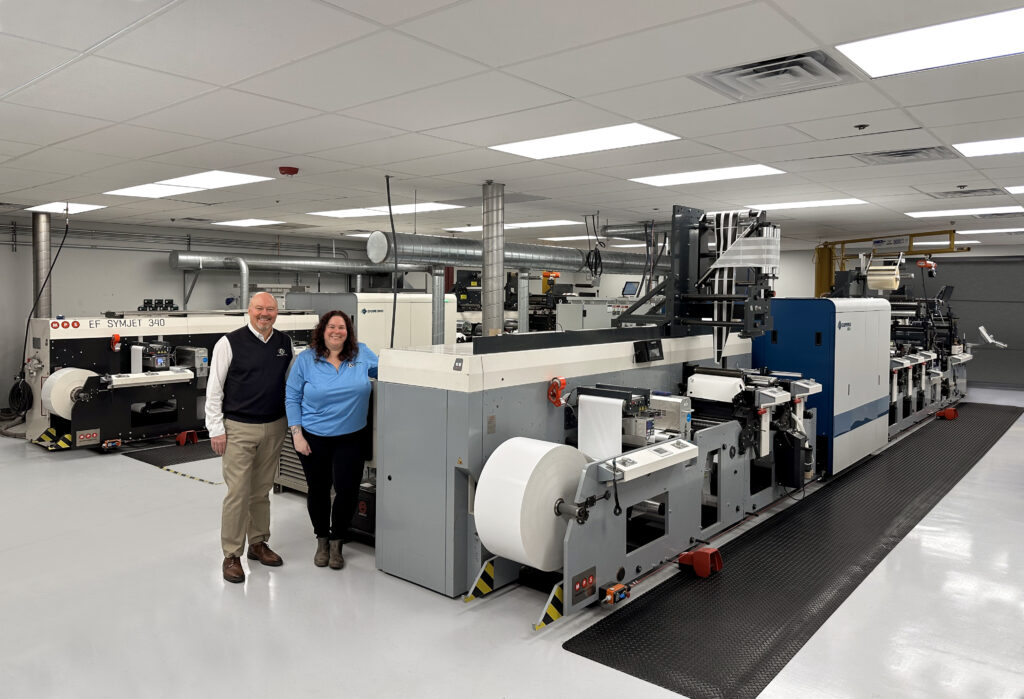